钢铁行业作为能源消耗大户,是国家节能减排工作的重点关注对象。同时,在我国当前市场竞争激烈的大形势下,钢铁企业面临着巨大的成本压力,而能源成本约占钢铁企业总成本的20%~35%,如何有效地降低能源消耗,提高余热余能的回收率,成为微利甚至亏损经营状态下的钢铁企业的一个重要利润增长点。因此,无论是对社会还是对钢铁企业自身来说,节能工作意义重大。
分析钢铁企业能源消耗水平,寻找其节能潜力点的一个重要方法是从企业的能源平衡着手,计算相关工序单位产品能耗和吨钢综合能耗等常用的能耗指标,对其进行对标分析和趋势分析。但是,目前我国钢铁企业的能源管理水平参差不齐,部分企业存在着能源计量体系不完善、能源平衡表内容不完整、能耗指标计算不准确等问题,这就需要企业能源管理人员要充分理解相关标准内容,掌握能耗指标的计算方法,并不断推动能源计量系统的完善,确保能源计量数据的全面和准确。
其中,能源平衡、能源计量是计算钢铁企业能耗指标的基础和起点,其面向的对象应尽可能细化到具体工序甚至主要用能设备,能源平衡表应尽量包含所涉及的全部能源和耗能工质,能源的折标准煤系数应尽可能立足于实测值。
工序单位产品能耗只有在具有相同系统边界时才具有可比性,现有标准对工序单位产品能耗计算的规定还可进一步完善,以更好地满足实际需要,并适应技术的进步。而吨钢综合能耗只能反映企业自身能耗水平的变化,在企业间缺乏可比性,片面强调该指标不利于企业和社会优化能源的利用。在计算吨钢综合能耗时,应注意计算方法的科学性、合理性,使其变化能够正确反映本企业节能降耗成果。
能源和耗能工质
在钢铁企业能耗指标计算中,纳入统计的能源种类除了通常意义上的一次能源和二次能源以外,还包括耗能工质,即在生产过程中所消耗的不作为原料使用、也不进入产品,而是在生产或制取时需要直接消耗能源的工作物质。常见的耗能工质有氧气、氮气、氩气、新水、软水、鼓风、压缩空气等。有的耗能工质同时也是二次能源,如乙炔取当量值时被视作二次能源,而在取等价值时被视作耗能工质。
在实际的管理过程中,有的钢铁企业是将电动鼓风、压缩空气等直接摊入各工序电耗。这样做虽然使统计工作得到简化,但却不便于从中分析用能的合理程度。
能源折标准煤系数
在计算能耗之前,各种能源和耗能工质的量都需要乘以各自的折标准煤系数折算成标准煤量。每千克标准煤的低位热值为29307千焦;一次能源的折标准煤系数为其低位热值与标准煤低位热值之比;二次能源的折标准煤系数分为当量值折标准煤系数和等价值折标准煤系数,其中等价热值折标煤系数考虑了由一次能源转换为二次能源的能量损耗。
在目前实践中,二次能源都采用当量值折标准煤系数,其中蒸汽是按其焓值折算。虽然有相关研究建议燃料能源的低位热值取统计报告期内的实测值,但是在实际的管理过程中,直接采用相关标准给出的参考值的现象比较普遍,并且对于不同压力、温度的蒸汽,通常都采用同一折标准煤系数,而忽略了其焓值的差异,这都会使计算出的能耗指标偏离实际值。
工序单位产品能耗计算
钢铁企业涉及的工序通常有焦化、烧结、球团、炼铁、炼钢、轧钢、石灰等,还有空分、动力、热电等辅助工序。其中,炼钢工序又可细分为转炉工序、电炉工序、精炼工序、连铸工序,而轧钢工序又可根据产品类型和规格进一步细分,如高线、棒材、中厚板、冷轧等。对于不同的钢铁企业,由于生产流程的差异而涵盖的工序有所不同。
确定了工序的能源消耗统计范围也就是确定了该工序作为一个能源系统的系统边界,通过该边界流入系统的能源即为能源输入,通过该边界流出系统的能源即为能源输出。对于有能源回收的工序,能源输出量等于能源回收量扣除回收的能源被工序自身消耗的部分,能源输入量等于能源消耗量扣除本工序回收的能源被工序自身消耗的部分。
钢铁企业中各工序回收的能源主要有蒸汽(或热力)、焦炉煤气、高炉煤气、转炉煤气、电力等。除此以外,焦化工序回收的能源还有焦炭、焦油、粗苯。
工序单位产品能耗一般可按下列公式计算:
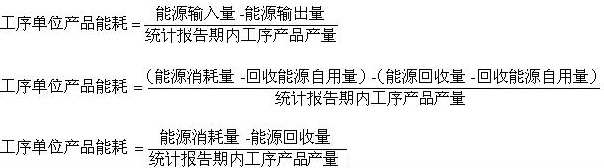
采用能源输入量和能源输出量计算工序单位产品能耗可以使计算得到简化,避免重复计算或漏记,但其不能进一步反映工序内部能源加工、转换和回收利用的情况,不利于分析工序能耗状况。而采用能源消耗量和回收量计算工序单位产品能耗则可以更为细致地反映工序能源消耗的状况,但其对能源计量体系的完善程度要求更高。
除了轧钢工序外,炼焦、烧结、球团、炼铁、转炉、电炉、精炼、连铸、石灰、空分等工序单位产品能耗在明确统计范围后是可比的,可以在工艺和产品类似的企业之间进行对标分析。为便于对标,《粗钢生产主要工序单位产品能源消耗限额(GB21256-2013)》《焦炭单位产品能源消耗限额(GB21342-2013)》对烧结、球团、炼铁、转炉、焦化等工序的系统范围都做了明确的界定。
在《粗钢生产主要工序单位产品能源消耗限额(GB21256-2007)》中,曾规定烧结工序的能源回收量既可以按回收蒸汽量计算,又可以按余热发电量计算。事实上,这二者之间存在着热电转化效率的差异。企业在计算烧结工序能耗时,一般选择蒸汽作为回收的能源,也有企业选择电力作为回收能源,但是在计算电力消耗时采用了当量值,而在计算电力回收时采用了等价值。在工程实践中,烧结余热发电系统的情况也往往比较复杂,有的是在发电的同时还向其他工序输出蒸汽,有的从外部调入蒸汽作为汽轮机的补汽,还有的采用了具有补燃功能的余热锅炉。如按回收电力计算能源回收量,在量和质上都难以准确反映余热回收的实际效果,导致计算出的工序能耗缺乏可比性。因此,在《粗钢生产主要工序单位产品能源消耗限额(GB21256-2013)》中,已经明确烧结工序的能源回收量按回收的蒸汽量计算。但是,当遇到余热锅炉具有补燃功能时或采用燃料燃烧过热蒸汽时,是将此项燃料消耗计入工序能源消耗,还是相应扣除蒸汽量,还有待进一步商榷。同样,干熄焦也常常兼具供热和发电的双重功能,在《焦炭单位产品能源消耗限额(GB21342-2013)》中有关干熄焦产出明确为蒸汽。
在高炉工序中,有的采用蒸汽拖动鼓风,也有的采用电动鼓风。由于蒸汽热能转化为机械能的效率要低于电能转化为机械能的效率,因此,如将鼓风用蒸汽或电计入工序能源消耗,也会使计算出的工序能耗缺乏可比性。近些年新出现的BPRT技术(煤气透平与电动机同轴驱动的高炉鼓风机技术),其作用直接体现在降低高炉工序用电,在计算高炉工序能耗时无需再扣除煤气透平所输出的机械能,而《粗钢生产主要工序单位产品能源消耗限额(GB21256-2013)》中尚未涉及此项技术。
另外,随着技术的进步,一些新的余热回收技术也逐渐被采用。如回收高炉冲渣水余热采暖技术和有机工质朗肯循环发电技术,其余热回收是否该纳入工序能耗计算以及该如何计算,目前还缺乏具体的规定,有待相关标准进一步完善。在未来,对于余热回收,应考虑将实际回收热量作为能源回收量。同样,得到具有可比性的工序单位产品能耗的前提,是对应工序范围内配备有足够的能源计量仪表用于采集所需能源消耗数据。
能源平衡与能源计量
钢铁企业的能源平衡是以企业内部的各工序或用能部门为研究对象,研究各类能源的收入和支出情况,对于企业的各种能源,无论是购入的还是自产的,都必须做到收支平衡。能源平衡表数据是钢铁企业计算工序单位产品能耗和吨钢综合能耗的基础。
钢铁企业能源平衡表的编制应尽可能覆盖所有能源,对于每一种能源,应如实反映能源的输入、输出、使用、库存变动及损耗等情况;对于研究对象,还应尽量细分,不但要将用能单元划分到工序或分厂级别,还要尽可能划分到某一工序的具体产线甚至某一用能设备,如炼焦工序的不同焦炉、烧结工序的不同烧结机、炼铁工序的不同高炉等。如此,才能通过能源平衡表深入分析企业内部耗能情况、查找节能潜力,明确改进方向。
但是,目前一些钢铁企业在编制能源平衡表时还存在不少问题。例如,有些钢铁企业的炼铁工序只在能源输出中体现了高炉煤气,而在本工序的能源消耗中却没有将高炉煤气纳入统计;有些钢铁企业的炼钢工序,转炉煤气和汽化冷却蒸汽除本工序自用外,其余全部放散,但在工序能源平衡中没有将其纳入统计。这样做,容易掩盖本工序在能源消耗上的不合理,增加了进一步判断节能潜力点和估算节能量的难度。还有些钢铁企业,其各单元合计的高炉煤气消耗量比炼铁工序高炉煤气输出量高出许多,用这样的能源平衡表计算工序单位产品能耗和吨钢综合能耗,预测这些指标的变化趋势将会出现较大的偏差。
能源平衡表的质量,仰仗于能源计量数据的准确度和能源计量体系的完善度,能源计量的基础作用体现在为能源管理提供充分、全面、准确、可靠的能源数据。目前,有些钢铁企业的能源计量管理还处于比较初级的阶段,存在着缺少专业的能源计量管理人员、能源计量器具配置不足,已有计量器具没有按期检定、校验、维护,准确度等级不达标等问题,很多能源消耗数据都是估算确定,从而影响了能耗指标的准确度和客观性。当前,国家明确要求钢铁行业必须建立能源管理体系并取得相关认证,《钢铁行业能源管理体系实施指南》(GB/T30258-2013)已于2014年7月1日开始实施,钢铁企业可以在建立能源管理体系过程中完善能源计量体系、规范能耗指标的管理。
吨钢综合能耗计算
钢铁企业吨钢综合能耗可按下式计算:

如无附加规定,钢吨综合能耗统计范围将覆盖整个企业。由于各企业之间生产流程和工艺的差异,吨钢综合能耗在企业间缺乏可比性,其变化只反映本企业能耗水平的进退,但有时吨钢综合能耗也作为行业的统一考核指标。
吨钢综合能耗反映了本企业自身能耗水平变化,但却不能反映企业在全社会范围内的合理用能程度。例如,当企业用自产焦炭代替外购焦炭时,会使企业吨钢综合能耗提高,但采用自产焦炭后,焦炭质量稳定,可促进后续炼铁工序的稳定生产和节能降耗。高热值的焦炉煤气和干熄焦所产蒸汽可以用于钢铁企业其他工序,而焦炉则可以使用廉价的高炉煤气。因此,片面强调吨钢综合能耗,反而不利于促进能源的高效利用,除非将焦炭的折标准煤系数统一采用等价值折标准煤系数。
与焦炭类似的还有石灰。钢铁企业在生产中要消耗大量的石灰,而石灰的生产也要耗费大量能源,但是目前石灰还没有被视作耗能工质,外购石灰的企业比自产石灰的企业可以达到更低的吨钢综合能耗。为此,很多企业在计算吨钢综合能耗的时候都扣除了石灰工序的能耗。但事实上,钢铁企业自产石灰可以充分利用其丰富的煤气资源,选用更为节能的气烧窑型,并综合利用余热,其能效明显优于独立的石灰生产企业。因此,在未来,可以将石灰视作一种耗能工质,采用等价热值折标准煤系数。
此外,对吨钢综合能耗影响比较特殊的还有热电工序。热电工序可以为企业提供蒸汽、电力、鼓风,钢铁企业热电工序的工艺设备类型也比较复杂,有纯燃或混燃外购能源(例如煤)的锅炉,也有纯燃煤气的CCPP机组(燃气蒸汽联合循环发电机组)和纯燃煤气锅炉,有的企业甚至将干熄焦、烧结余热发电以及饱和蒸汽发电机组也纳入热电工序。燃气锅炉作为煤气的调节用户,对实现煤气零放散具有重要作用,而钢铁企业燃煤热电机组一般容量小、参数低、发电煤耗高,且又会增加企业外购能源消耗,因此,有逐渐被淘汰的趋势。
利用企业的富余煤气和余热发电,在降低企业能源消耗的同时,还具有相当高的经济效益,是企业降本增效的重要手段。但是,由于在计算吨钢综合能耗时电力一般取当量热值,这使吨钢综合能耗下降幅度较小。有的企业在计算吨钢综合能耗时,将热电工序排除在外,并从企业总能耗中扣除了热电工序的能源损失(热电工序能源输入量-热电工序能源输出量),即将热电工序的能源输入作为企业能源输出的一部分,而将热电工序输出的蒸汽和电力作为企业能源输入的一部分,这样会导致因热电工序能效提高而使吨钢综合能耗上升,扭曲了热电工序节能工作的作用。相对合理的做法是,将热电工序中燃煤气和余热回收部分还保留在企业能耗统计范围之内,而只将燃煤部分排除在外。