20世纪末是铁矿球团(以下简称球团)发展的鼎盛时期,焙烧设备中的带式焙烧机(以下简称带式机)、链箅机—回转窑(以下简称回转窑)各具特点,竞相发展。21世纪初,中国回转窑球团得到大发展,产能达到1.7亿吨。当前,在淘汰落后产能中,由于带式机投资省,显现出很大的发展空间。
带式球团的发展
20世纪50年代,球团投入工业生产;90年代,球团发展到鼎盛时期,规模达到3亿吨。焙烧设备从简单的竖炉发展到带式机、回转窑,其中带式机占55%。21世纪初,中国回转窑球团大发展。到2012年,球团规模达到2.4亿吨,其中,回转窑球团产能达到1.7亿吨(占71.5%),竖炉产能达到0.38亿吨(占24%),带式球团产能仅为0.07亿吨(占4.5%),但每年仍要进口几千万吨球团矿。当前,钢铁产业结构调整,球团是仍在发展的产业,其发展的趋势很有可能转向带式球团。首钢曹妃甸400万吨带式球团投产,包钢新建500万吨带式球团,显示出这种趋势。
球团工艺技术经济对比
3种工艺球团工程技术经济对比见表1。由表1可得:一是竖炉球团单机产量低,质量较差,很难满足大高炉冶炼要求,不宜使用赤铁矿精矿,环保治理难度大。二是带式机和回转窑两者的产量、质量均优。但是,相较而言,带式机原料适应能力最强,各种原料皆可,回转窑对赤铁矿适应较差;带式机燃料用天然气、焦炉煤气、重油,不能用煤,能耗为82.4元/吨。三是回转窑用煤,而油、气价格比煤高5倍~8倍,虽然回转窑燃耗高、电耗高,但是,能耗为29.9元/吨,比带式机低很多。因此,燃料问题成为带式球团发展的软肋。四是带式球团投资比回转窑省。带式机设备材料费用低,粉尘量小,总费用低,而回转窑设备材料费用高、粉尘量大,总费用高。因此,带式球团投资低,虽然生产运行费用高,但如果解决燃料问题,带式球团有望得到充足的发展。
带式机燃料选择
目前,带式球团燃料为天然气、焦炉煤气、重油、混合煤气(发热值12.1MJ/m3),不能直接用煤。导致带式球团生产运行成本高出回转窑(用煤)几倍。带式机工艺可将煤转化为发生炉煤气(煤制气),成本较低,再用部分重油(或者天然气),技术可行,投资成本低,便于实施。以120万吨带式球团为例,使用天然气、焦炉煤气、重油、煤制气重油几种燃料方案进行比较。球团热量消耗和燃料用量见表2和表3。带式球团各种燃料费用和投资比较见表4。由这些表可见:煤制气重油方案燃料费用最低,一年即可收回投资,每年可节省几千万元燃料费用。
煤制气重油方案是用烟煤生产发生炉煤气(煤制气),与重油(或者天然气)混合喷吹,作为球团燃料。混合物的配成比为:80%煤制气,20%重油。气、油混合物发热值为12.7MJ/Nm3(3050kcal/kg)。
煤制气工艺是合格煤由电动葫芦提升至主厂房上煤层,卸至每个发生炉的储煤仓,储煤仓的煤再经自动加煤机加入炉内,煤受到来自气化段煤气的加热而干馏,干馏后的半焦下移到气化段与气化剂反应生成煤气(气化剂由空气、蒸汽组成)。气化段生成的煤气分为两部分:一部分从两段炉下段煤气出口出炉,进入旋风除尘器后进煤气汇总管道;另一部分向上在干馏段生成煤气从上段煤气出口出炉。上段出口的煤气先进入电捕焦油器除焦油后与下段煤气混合,在煤制气工艺中,电捕焦油器除掉的焦油是低温干馏产物,进入焦油池。煤气站投资估算为1800万元(其中设备费用约1100万元)。
重油发热值为38MJ/kg,重油用量为4373t/a。重油设施有重油站和供油站。重质原油由运油车运输至重油站,通过油泵房中卸油泵卸重油于重油罐中存储,油罐中的重质原油通过供油泵输送至带式焙烧室的地下油罐,再通过油泵抽送到带式焙烧炉燃烧室使用和精矿干燥。重油设施投资估算为450万元(其中设备费用为300万元)。
120万吨球团工程煤制气重油方案技术经济指标见表5。
目前,发展球团符合钢铁产业结构调整方向,也是球团内部淘汰落后产能(大约20%)所必需的。带式球团由于投资低,适应各种原料,可能成为球团发展的方向。但带式球团使用油、气为燃料,运行成本很高,制约它的发展。利用资源丰富、价格低廉的煤(按相同发热值与油、气燃料相比)生产煤制气,再配以20%的重油(或者天然气)作为带式球团的燃料,技术可行,成本大幅降低,比用油、气降低50%以上,从而消除带式球团发展的一个重要障碍。
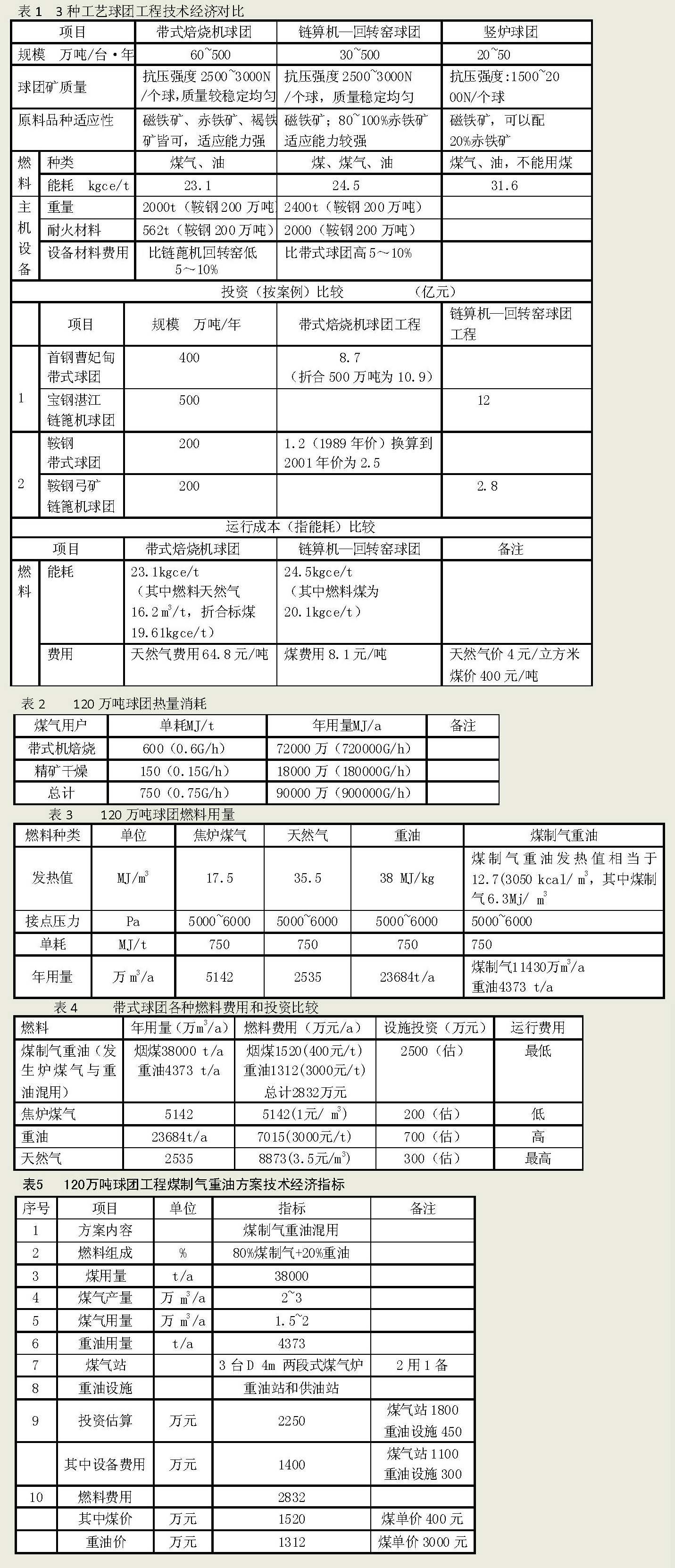