烧结烟气是长流程钢铁生产中最主要的废气污染源,其温度偏低、废气量大、污染物含量高且成分复杂。据统计,烧结工序能耗约占整个钢铁生产总能耗的12%,其SO2、NOx、CO2、粉尘排放量分别占钢企总排放量的40%~60%、50%~55%、12%~15%、15%~20%,是钢铁行业低温余热利用和废气治理的难点和重点。
当前,烧结烟气治理技术首推脱硫。按照脱硫产物的干湿形态,烟气脱硫可分为湿法(石灰石/石灰—石膏法、氨法、镁法、离子液法、海水法、双碱法)、半干法(LJS循环流化床法、ENS法、NID法、SDA旋转喷雾干燥法、MEROS烧结污染物最大化降减法、密相干塔法、GSCA双循环流化床法、电子束照射法、LEC石灰石烟气净化法、CSDI荷电干式喷射脱硫法、PPCP脉冲电晕法等)和干法(活性炭法)。从调研数据分析,湿法、半干法、干法工艺在180平方米以下烧结机中分别占65%、30%、5%,在180平方米以上烧结机中分别约占55%、40%、5%。近年来,污染物协同治理的活性炭工艺在大型烧结机上的应用呈加速趋势。对于不同的烧结烟气一体化净化工艺,钢铁企业应结合各自企业的烟气温度、烟气量、污染物浓度等参数,以及烧结机工况、场地条件、治理要求、投资,还有运维成本、地区因素等,合理选择烧结烟气综合治理方案和技术。
设备运行效果比较
经过多年的探索和长期的工程实践,石灰石/石灰—石膏法、循环流化床法、旋转喷雾法等工艺由于在运行稳定性和经济性方面具有一定优势,得到钢铁企业的认可,烧结烟气脱硫主流工艺逐渐形成。企业脱硫设施的运行经验不断积累,环保部门针对脱硫设施减排效果的监管能力明显提高,全国烧结SO2减排工作推进显著,累计实现SO2减排超过60万吨。
从表1中可看出,各种脱硫工艺都有其特点和适用性,运行成本也有较大差别。例如,石灰石/石灰—石膏法运行成本低,工艺适应性强,但占地大、塔内构件易腐蚀、磨损,管路易堵塞,另有废水排放和烟囱雨的问题;氨法存在氨逃逸、硫铵结晶难、副产品市场化、二次污染等问题;循环流化床法运行费高、操作难度大、副产物不易利用,同时由于烟气量波动常会引起吸收剂的流化状态不稳定,出现堵塞、失流、塌床等现象;氧化镁法受制于脱硫剂品质,还要解决好副产物利用和系统防腐、施工成本高的问题;活性炭技术运行费用过于昂贵,对烟气温度和SO2浓度有严格限制,控制和管理要求较高,硫资源回收处理等辅助系统复杂;离子液法流程长、废水处理量大,对入口烟气SO2浓度有要求。
钢铁企业进行技术路线选择时,应根据各自情况和脱硫技术工艺特点、经济指标、工程条件、国家政策等酌情而定,要综合考虑技术先进性、工艺可靠性、运行风险、投资和运行成本、占地和烟气处理能力、副产物利用难易、多种污染物协同处置能力、与烧结工序附属设施的优化配置等因素。
设备运行问题和改进方向
回顾国内烧结脱硫历程,几乎所有钢铁企业运行的脱硫设施多少都存在技术不成熟、投资大、运行成本高、故障率高,以及副产物难利用、产生二次污染等问题,笔者分析主要原因,梳理如下:
一是单纯照搬火电脱硫工艺,未针对烧结烟气特点,进行特别优化设计,导致工艺不稳定,综合脱硫效率低,运行成本高;二是脱硫工程设施建设不规范,偷工减料、低质低价现象严重,关键设备选型或加工技术不当,造成先天不足;三是日常运行维护不当,甚至随意停开,造成脱硫设施非正常损坏;四是在线监测不规范,仪器仪表成为摆设,偷排漏排问题突出;五是实际脱硫效率低,对多种污染物的协同处理能力考虑不足;六是脱硫副产物以消纳、处置为主,易造成二次污染。
针对已存在的问题,笔者认为,未来的改进方向如下:
一是开展烧结脱硫设施后评估工作,加强已建设施的日常监测和后续跟踪核查;二是在行业积极引导、有序推进成熟脱硫技术的工程化应用;三是烧结脱硫建设过程加强监管,杜绝粗制滥造的豆腐渣工程;四是取消旁路设施,尤其针对在线监测设施方面要建立健全核查制度;五是从硫污染总量减排转向硫资源捕获利用和多种污染物的协同控制上来;六是加大处罚力度,公布违法违规企业名单;七是将烧结脱硫副产物的利用纳入钢铁企业固体废物综合利用体系中,积极探索脱硫副产物的利用途径。
烧结烟气综合治理技术的发展方向
目前,烧结烟气处理的工艺方法很多,但研究主要集中在烟气除尘和脱硫上。随着人们对大气污染物排放的要求越来越高,选择适合的烟气净化工艺,实现脱硫、脱硝、脱二噁英、除尘的一体化综合治理,已势在必行。在这方面,日本钢企主要采取活性炭吸附工艺(太钢已应用),欧洲西门子奥钢联开发了MEROS工艺(马钢已应用),以色列Lextran公司开发了催化氧化烟气综合清洁工艺,我国龙净环保在循环流化床工艺基础上喷入脱硝剂强化脱硝效果,宝钢股份拟在4号烧结机技术改造上采用循环流化床+SCR工艺。
由表2可见,活性炭工艺最为成熟,具有五合一(脱硫、脱硝、脱二噁英、脱重金属、脱酸性气体)协同净化功能,但存在脱硝效率低、运行成本高、设备庞大且造价高、腐蚀问题突出、外围系统复杂、活性炭反复使用后吸附率降低消耗大、活性炭再生能耗较高等问题。MEROS工艺简单,入口温度要求低,温度变化适应性好,但年运行费相对较高,不能控制烧结烟气中的NOx,在控制二噁英的同时会产生混有二噁英的固体废弃物。LJS—FGD工艺对烟气量和烟气成分具有良好的适应性,塔内结构简单,烟气无需再加热,但脱硝效率低,副产物的应用范围有待进一步拓宽。S-SCR工艺灵活性强、安全性高、可利用已建脱硫装置实现脱硫、脱硝、脱二噁英一体化,装置占地小、阻力低、系统简单、操作便利,脱硝效率可达80%以上,二噁英完全分解,无二次衍生污染物产生,缺点是催化剂因中毒活性会逐渐降低,更换催化剂成本较高。催化氧化烟气综合清洁技术单位烧结矿运行成本低,还可同时实现脱汞,其脱硫、脱硝效果好,运行稳定,可利用焦化厂废氨副产硫酸铵或硝酸铵化肥,但过程中有废水产生,且有机催化剂需进口,尚未国产化,价格较高。
从宝钢在烧结烟气治理领域的实践来看,2004年,宝钢启动了烧结烟气综合深度净化治理(脱硫、脱硝、脱二噁英以及微细粉尘治理)等方面的技术开发和工业试验。目前,宝钢拥有烧结脱硫装置10余套,脱硫工艺包括:气喷旋冲石灰石—石膏法、循环流化床法、旋转喷雾法、氧化镁法等。这些脱硫设施均能有效脱除烧结烟气中的SO2,其脱硫率和同步运转率均能达到90%。但随着环保压力的不断加大,除脱硫外,宝钢还需要进一步采取措施,继续脱除氮氧化物、甚至是脱除二噁英等有机污染物、汞、重金属、PM2.5等,以满足不断升级的环保要求,必须尽快开发出投资运行成本低廉的,联合脱硫脱硝脱二噁英的烧结烟气综合净化新技术,同时必须兼顾资源回收和副产物综合利用的问题。目前,宝钢正开展活性炭法一体化工艺、烟气脱硝、脱二噁英、微细粉尘和无组织扬尘方面的研究,并将在宝钢股份和宝钢湛江实现产业化应用。
据上分析,结合我国国情和大部分企业烧结脱硫设施已建成的实际,笔者认为,未来烧结烟气污染物协同治理较有竞争力的发展方向可能为———采用烟气循环技术(内循环/外循环)减少烟气量和污染物排放,经高效电除尘后,再结合脱硫脱硝一体化净化技术(如活性炭工艺、石灰石/石灰—石膏法/循环流化床/旋转喷雾法脱硫+SCR工艺)对烧结烟气进行深度治理。
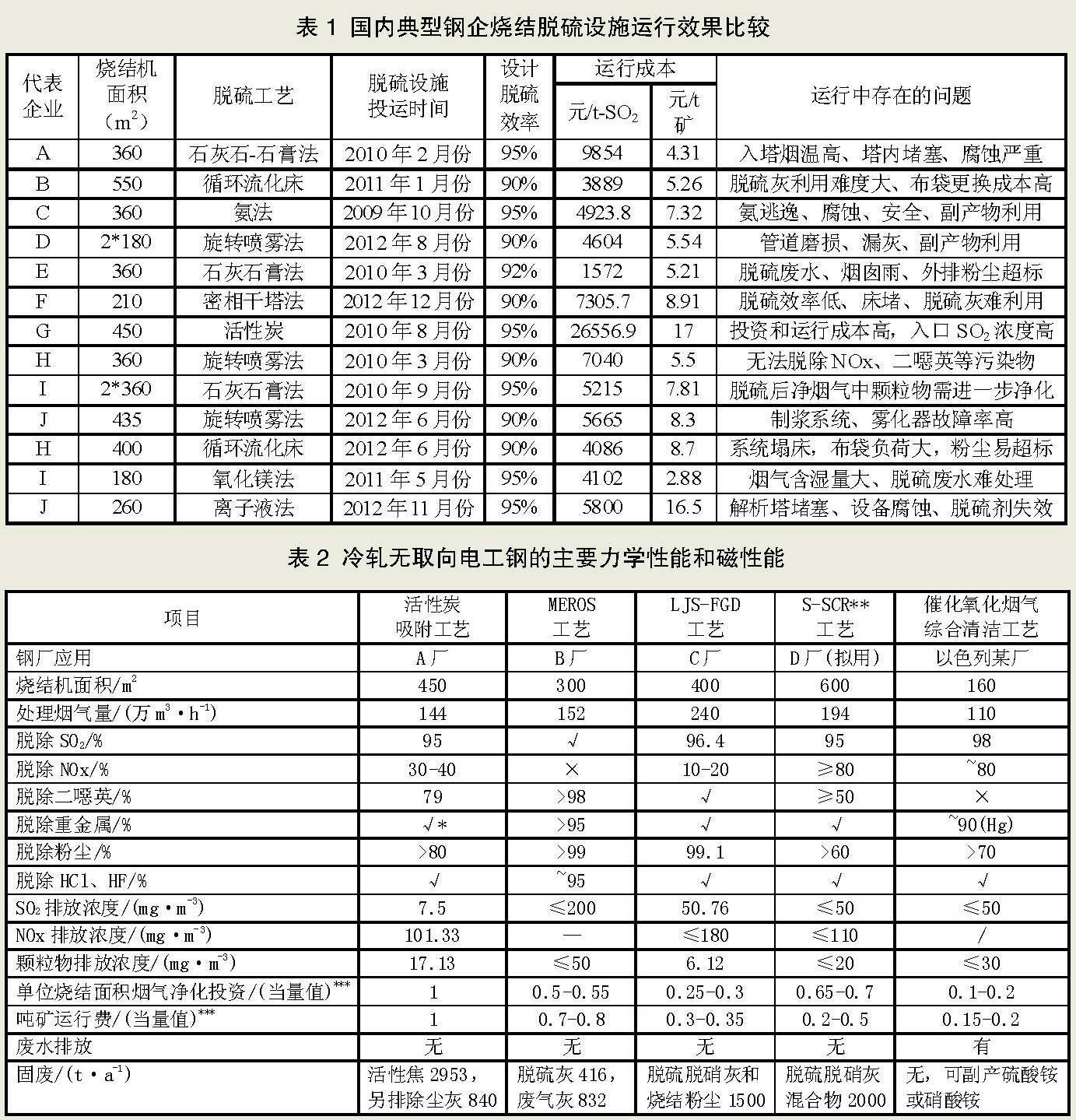
备注:表中“—”表示无具体数据;“√”表示无具体数据,但有定性结论。
表中标注“*”处,指S-SCR工艺的相关数据为设计值。
表中标注“**”处,是以甲厂为基准,费用折算的当量值。