近年来,随着进口矿粉成分的劣化及企业降低成本的压力加大,首钢京唐烧结使用固废和非主流的比例逐步提高,给烧结生产带来一定负面影响,如SiO2和Al2O3含量增加、成品率下降。尤其2013年初提高非主流矿粉配比后,尽管降成本效果显著,但碱金属和Cl含量的升高也给烧结和高炉生产带来了压力。同时,随着近年来对环境和烟气治理问题的持续关注,烧结工序作为钢铁企业污染物大户也备受关注。为了实现烧结过程中对资源的高效利用,为高炉提供质量优良、稳定的烧结矿,首钢京唐烧结开展了一系列工艺、设备攻关工作,取得了一定成效(首钢京唐烧结矿指标改善情况见附表)。
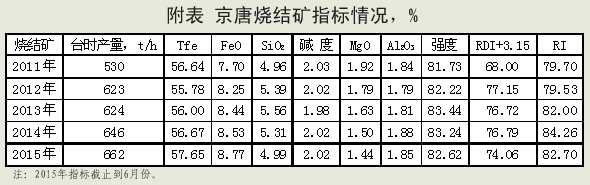
原料劣化情况
非主流矿粉用量提高。2012年,首钢京唐烧结混匀大堆使用三大矿业巨头的主流矿比例在80%水平,2013年1月~4月份降低到70%水平(最低约67%),降低了约10个百分点;非主流矿粉平均K含量是主流矿的14.9倍,Na含量是7.4倍,Zn含量是3.5倍,Cl含量是6.4倍。非主流矿粉配比的提高,不仅使烧结矿有害元素含量升高(不利于高炉长寿),同时使烧结过程出现了箅条黏结加剧、白灰消化变差等问题。
主流矿粉成分劣化。除了非主流矿粉使用比例提高外,主流矿自身的成分也在逐步劣化。例如,巴卡粉的TFe含量从67%水平降低到64%~65%,SiO2含量从1%左右增加到2.8%。
矿粉粒度劣化。此外,除了成分劣化外,近几年矿粉的粒度也呈现劣化趋势,特别是有些矿粉的粒度粗化。虽然大粒度矿粉有利于改善烧结透气性,但粒度过大对于烧结制粒和反应均不利,大粒度矿在烧结过程中经受的反应、液相生成和流动状况与细混匀矿均有差异。更为关键的是,烧结布料时,大粒度矿易偏析分布在烧结料层下部,这对烧结矿质量的均匀性造成很大负面影响。在首钢京唐烧结料层厚度810mm条件下,大粒度矿可能造成两种负面效果:一是破坏制粒过程中小球的正常成长;二是成分和粒度偏析严重,对烧结矿质量造成较大负面影响。
烧结技术进步一览
铁矿粉高温原位观察研究。2011年首钢京唐烧结用巴卡粉在10%~15%的水平,增加巴卡粉配比以提高烧结矿品位,存在对烧结过程液相流动性降低的担忧。研究人员采用微型烧结方法,借助高温激光共焦显微镜(CSLM)和热重—差热设备(TG-DSC),观察了铁矿粉和CaO在烧结过程中的反应过程,并将巴卡粉与杨迪粉等进行了系统对比,发现在有充足的CaO条件下(Ca:Fe=1:1),巴卡粉表现出不弱于杨迪粉的流动性。同时基础研究发现,1190℃—最高温—1160℃这段烧结高温历程对于烧结矿质量很重要。基于研究结果,他们认为,增加巴卡粉到20%以上对烧结矿质量有利,2012年初在首钢京唐烧结进行了增加巴卡粉的工业试验;其比例从13%提高到21%后,烧结矿指标得到改善。从2012年到2015年,首钢京唐烧结用巴卡粉比例基本保证在20%以上水平。
料层分区测定研究。2009年投产后首钢京唐烧结料层厚度很快即达到800mm水平,随着近几年进口矿粉粒度的粗化,给800mm厚料层烧结带来难题。2012年在首钢京唐进行的吊取台车分层测试发现,1号机台车上物料的碱度从第一层的2.1偏析到第四层的不足1.7水平。过大的偏析不利于获得优质黏结相,致使下层烧结矿质量较中层有所变差,不利于发挥厚料层优势。料层分区研究表明,不同烧结机物料分布所面临的问题不同,故采取了不同的方法予以应对,取得了不错的效果。
单辊导料槽增设耐材保护。首钢京唐550m2烧结机从机尾落到导料槽表面的落差高,导料槽所受烧结矿的冲击力、所受高温烧结矿的摩擦力均较大,导料槽寿命一般在3个月~4个月。对此,首钢京唐提出在导料槽料衬表面敷设耐火浇注料的思路,利用耐材耐高温、耐磨和隔热等性能来缓冲烧结饼下落的冲击力和接触高温热传导,进而延长导料槽寿命。2013年4月首钢京唐2号烧结机导料槽进行了整体耐火材料浇注改造,新导料槽至2014年5月年修时使用寿命已达1年,较过去3个月~4个月的使用寿命大幅延长;同时,因导料槽造成的检修次数明显减少,烧结机作业率提高。同时,这一改造减少了烧结矿直接撞击导料槽金属结构,对成品率和强度也有利。
基于加导流板的优化环冷配风等工作。2013年提高非主流矿使用比例后,首钢京唐烧结自返矿比例升到30%~32%(6.3mm筛)。为降低烧结返矿、提高烧结产量,研究人员从改善环冷机上烧结矿的冷却入手,针对580m2环冷机鼓风机开展了配风研究,提出增设导流板的优化配风改进方案。通过加装导流板,可改善风箱内的风量分配和速度场、压力场分布,有利于减少环冷机内外环的冷却偏差,减少局部急冷现象,并减少气体在风箱内的涡流损耗。2013年4月,2号机进行配风改造后,烧结矿冷却均匀性得到提高,返矿率降低了约2%。在2号机配风改造成功基础上,2013年10月底在1号环冷机上进行了推广改造。
自然镁烧结。随着矿粉品质的劣化,烧结矿中SiO2和Al2O3质量分数逐步呈现升高趋势,且由于成本压力而难以控制。MgO作为“主动”配加的原料,一定程度上具备可控性。如果能在保证烧结矿质量、高炉顺稳基础上降低烧结矿MgO,则可提高烧结矿品位,发展优质铁酸钙黏结相。2012年首钢京唐烧结进行了减少白云石配比的实践,烧结矿MgO含量逐步从2.0%降低到1.3%(在消纳企业含镁固废资源后处在1.3%~1.5%),实现了自然镁烧结。整体上看,烧结矿MgO含量降低0.5%,有助于提高烧结矿TFe品位0.28%;与此同时,停配含镁熔剂后,烧结过程中耗热减少,液相流动性改善,烧结矿质量得以提升,冶金性能未有恶化。同时,低镁烧结矿搭配含镁球团矿后,高炉综合炉料熔滴性能得到改善。
箅条黏结防治和有害元素控制。烧结机台车箅条之间的间隙是烧结抽风的主要通道,生产工艺要求箅条风道通畅而不能堵塞,否则会造成烧结机的有效抽风面积降低、烧结过程中风量分配不均匀,造成烧结机产质量下降。首钢京唐烧结2号机2013年4月年修发现箅条黏结严重,有害元素的升高是箅条黏结加剧的重要因素之一。基于此,首钢京唐烧结采取了如下攻关措施:一是优化配矿结构,通过控制非主流矿粉和固废使用比例来控制K和Cl带入量;二是适当调整铺底料厚度和粒度,烧结箅条黏结现象大为缓解。
熔剂结构优化。2014年为进一步降低烧结矿成本和改善烧结矿质量,在取消配加白云石后,首钢京唐继续从熔剂结构入手,提出了自产高钙白灰搭配钢渣替代外购白灰的技术思路。2014年首钢京唐将套筒窑白灰生产模式由2个高钙窑
2个普通窑改为4个高钙窑,富余部分高钙白灰供烧结配用。烧结增配活性较高的自产高钙白灰,与提高钢渣配比同步进行,有效降低了外购白灰的消耗。熔剂的减量化,给烧结带来品位提高、熔剂有害元素带入减少等好处。
存在的问题及展望
尽管首钢京唐烧结取得一定的技术进步,但仍存在如下问题:
烧结采用新技术的程度不高。虽然在国内首先实现了800mm料层烧结和烧结智能闭环控制,但是,近几年来,与先进烧结厂相比,首钢京唐在烟气综合治理、大烟道烟气循环、选择性制粒等技术应用方面存在差距。
关于炉料结构中烧结矿和球团矿的最佳使用比例问题,仍须结合企业自身情况继续进行探索。这点在首钢京唐上二期项目的背景下更须要考虑。
烧结为了保证RDI指标,喷洒了CaCl2溶液,但从长远看,这不符合环保、设备长寿和节能减排的要求。应强化工艺攻关,提高烧结矿RDI指标。近期,首钢京唐已停止了CaCl2溶液喷洒。
烧结消纳固废等劣质资源和适应原燃料质量波动的水平仍待提高;烧结利用钢铁企业废弃物已达到80kg/t的较高水平,但仍须对不同固废进行更深入的研究,提出更合理的使用措施。
烧结指标有待进一步改善,烧结余热利用水平仍须提高。改善烧结矿质量、降低消耗和减少污染、提高烧结工序效率是提高烧结竞争力的根本。
应进一步强化烧结配矿、工艺和设备的联系、协作,进一步提高作业率,为高炉提供质量优良的烧结矿。