首钢京唐钢铁厂是按照循环经济理念建设的新一代可循环钢铁厂,为了实现5500m3巨型高炉的稳定生产、优化炉料结构、提高精料水平,设计并应用了国内首条504m2带式焙烧机球团生产线,构建了“高效率、低成本、节能环保”球团生产线,满足了2座5500m3巨型高炉高效低耗生产对炉料的要求。首钢京唐球团厂于2010年8月投产以来,经过4年多的运行,已经完全达到设计水平,年作业率达到98%以上,球团品位达到65.95%,球团抗压强度≥3000kN,工序能耗为17.11kgce/t,达到同类技术的国际先进水平(与国内外先进球团生产线的指标对比见附表),环境效益和社会效益显著。
工程设计研究与创新
优化工艺流程。工艺设计基于冶金流程工程学理论和首钢京唐钢铁厂的建厂理念,以流程优化、功能优化、结构优化、效率优化为目标,以动态精准设计为指导思想,注重工艺系统的顶层设计和物质流、能量流、信息流的协同高效运行,构建了以“流”“流程网络”“运行程序”为基本要素的新一代球团厂动态精准运行体系。设计注重原料准备工序的精准设计,为精准配料及高质量、多品种球团提供了多种调节方式,突出了造球、预热、焙烧、冷却、工艺风机等主工序的功能解析和高效集约化配置,为高效、低耗、优质、清洁的绿色球团生产奠定了基础。
工艺设计对工艺流程、功能集成、集约高效、布局紧凑方面进行了大量研究,对预配料、干燥、辊压、熔剂与燃料制备、配料、混合、造球、焙烧、冷却到成品分级等多工序进行紧密衔接,最大限度地缩短物流运距、减少物料转运,将功能相同或相近的建筑物联合设置,以减少占地面积,实现了连续紧凑。
优化工艺技术。设计采用国际先进的带式焙烧机工艺,焙烧机全长为126m,台车宽度为4m,台车面积为504m2,料层厚度为400mm,球团生产能力为400万吨/年。
提高热风利用率。带式焙烧机集7个工艺区段于一体,通过台车的循环运行,台车上的生球依次完成干燥、预热、焙烧、均热和冷却过程。干燥段分为鼓风干燥段和抽风干燥段,鼓风干燥段主要是利用二冷段热风对生球进行脱水干燥,抽风干燥段是通过回热风机抽取的预热段和焙烧段的热风对生球进行干燥。在预热段和焙烧段利用冷却1段热风和外部热源加热,在均热段不再使用外部热源,主要是利用球团自身放热和冷却1段的热风。合理的回热风利用系统最有效地实现热的再利用,高效短捷的流程将散热面积降到最低,有效降低了热耗,提高了能源循环利用率。
合理利用钢厂二次能源。不同于国外采用重油或天然气为热源,该项目焙烧机采用焦炉煤气作为外部热源。在固定的炉罩上设置32组烧嘴,通过流量的灵活调节实现工艺温度的灵活调节,最大限度地适应不同原料的需求,与此同时可以实现钢铁厂副产煤气的高效化利用,使高热值煤气得到最优化的利用,实现能源高效转换。
系统调控灵活。焙烧工序依靠工艺风机系统平衡焙烧机各个工艺段的温度和压力。工艺风机系统采用变频调速风机及自动控制阀门,实现各个工艺段温度的灵活调节和热量的合理分配。该系统通过先进可靠的造球系统保证生球入炉强度,减少烟气含尘量,有效延长风机使用寿命。
提高台车作业率。带式焙烧机工艺采用铺底料循环系统保护台车,以延长台车耐热件的使用寿命。头部设置更换台车装置,可以实现在5分钟之内台车的在线快速更换,离线维修,有效提高了台车的作业率。
采用内配固体燃料工艺。为了提高球团质量,该项目设计了熔剂与燃料制备工序,配置了内配固体燃料、内配白云石工序,预留根据不同原料调整燃料配比和生产熔剂性球团的手段。内配燃料工艺可以增加球团的孔隙率和还原性,这种球团用于高炉生产能提高生产率和降低焦比。这种高气孔率、高还原性的球团还能有效降低燃料消耗,降低焙烧机篦床温度以及风机的电耗。
在工艺设计中,该项目首次将熔剂与燃料制备系统布置在配料室旁边,将熔剂与燃料收集器置于配料室料仓的顶部,直接将熔剂粉、燃料粉输送到配料料仓中,通过优化流程有效简化了设备配置。熔剂与燃料制备系统中采用热废烟气自循环新工艺,以降低系统热耗,降低热风炉设备规格及投资,减少废气排放量,有利于节能环保。
开发球团往复式布料技术。该项目研究开发了新型球团专用布料胶带机,将往复式布料器与造球盘下的集料皮带集成为一条皮带,通过控制布料器头轮直径及高度,将生球落料高度控制到最小;通过布料器往复行走,实现生球单行程布料,有效减少生球的转运次数和落差,提高生球粒度合格率,布料均匀两侧无堆积。先进的布料胶带机宽胶带
双层辊筛布料工艺,保证在带式焙烧机上生球料层均匀一致,具有较好的透气性。
开发应用大型矿粉干燥窑。该项目开发了大型球团干燥窑技术,设计研制了国内特大型ф5m×22m 矿粉干燥窑,满足控制物料水分的要求。该项目相比常规的球团生产工艺配置,增加了原料干燥、辊压工序,确保球团精矿粉水分稳定、粒度及比表面积的均匀,提高其成球性,进而提高生球强度和质量。
研究开发大型造球系统。为确保造球效果,该项目在国内首次开发出最大规格的ф7.5m新型造球盘与大型带式焙烧机相配套。与常规ф6m造球盘相比,单机造球能力大幅度提高;圆盘直径加大,增加球团滚动次数,改善造球效果,提高生球强度;通过规模化造球,造球盘数量减少,厂房占地减小,工程造价降低。
集成创新应用大型技术装备。为与504m2的大型带式焙烧机相匹配,该项目首次采用了ф1700mm辊径的辊压机、600m2电除尘器及叶轮直径为ф3.6m的耐热风机,其中600m2电除尘器是国内单台除尘面积最大的电除尘器;主要工艺风机实现国产化,解决了以前球团大型风机由国外引进的问题。所有工艺风机均采用高压变频调速,控制调节方便,有效降低电耗。
台车运动力学研究。台车是带式焙烧机核心设备中的最关键的设备,台车总重量约占整个焙烧机总重量的17%。由于难于通过直接测量,检测台车在工况下温度和应力分布变化,只能通过已知条件建立模型、编制专门的程序,模拟台车在整个循环中的温度和应力分布情况。在此基础上,该项目使用ANSYS软件进行有限元应力分析,分析台车的失效形式;根据台车热工条件,通过三维设计和热应力有限元分析,合理确定台车和篦条的结构。
创新采用自润滑辊套技术。借鉴近年来在烧结台车上的成熟的自润滑轴承技术,台车辊轮轴承采用自润滑轴承结构,具有制造成本低、制造周期短、使用寿命长的特点,可以有效地降低维护成本,提高了焙烧机的作业率。自润滑轴承机体上嵌入由二硫化钼和二硫化钨组成的固体润滑剂,在摩擦过程中润滑剂微粒吸附在金属表面,起到润滑作用;在使用过程中无需添加油脂,实施免维护,而且使用寿命长,能够有效降低设备维护费用。
开发风箱端部及隔断密封技术。在生产实践中,为了进一步改善系统密封性,该项目通过对风箱端部及隔断密封工作条件的深入研究,优化设计了新型带式焙烧机的风箱端部及隔断密封装置,有效地提高密封效果,降低了系统漏风率。在生产实践的基础上,对带式焙烧机炉罩与台车间的密封效果进行分析,采取针对性改进措施,开发了新型炉罩与台车间的密封技术,进一步提高密封效果。
节能环保技术研究开发
首钢京唐球团秉承节能减排、绿色环保的先进理念,采用带式焙烧机球团生产工艺,在节能减排、清洁生产和循环经济等方面创新采用了多项先进技术,节能环保技术优势显著。主要表现在:一是带式焙烧机在一个密闭炉罩内完成干燥、预热、焙烧、冷却的全部工艺,同时带式焙烧机整体布置在一个封闭厂房内,有效减少粉尘泄漏。二是炉罩高温热风直接回用,管道距离短,回风管道面积大,热量利用效率高。炉罩采用多层耐热材料和保温材料,有效减少表面散热,降低热耗。工艺风机全部采用高压变频调速,降低电耗。三是全部除尘灰均采用浓相气力输灰系统返回配料室使用,充分回收和利用资源。输送设备和管道实现全密封,避免了传统除尘灰输送过程中产生的二次扬尘,极大地改善了工作条件和厂区环境。四是首次开发的矿粉干燥窑上采用专门研制的高效扬料板,采用高温旋风配风装置,提高热交换效率,增强干燥效果,减低热耗。
在设计研究中,该项目建立了基于能源高效转换的能量流网络和运行体系,实现系统节能;以“减量化、再循环、再利用”为用能准则,建立能量输入—输出模型,实现优化用能。主要技术创新包括:一是利用钢铁厂自产的焦炉煤气作为球团焙烧的燃料,优化燃料结构,取代了高热值天然气,使钢铁厂能源流结构得到优化,焦炉煤气的效能得到高效化的利用。二是开发研制适用于焦炉煤气的燃烧器,设计合理的燃烧器结构,实现低空气过剩系数调控,保证燃料燃烧完全和足够的火焰温度,降低CO2 和NOx的大量产生和排放,实现高效清洁燃烧,减少污染物排放。三是合理设置燃烧器安装位置和数量,以满足球团焙烧工艺为前提,实现燃烧和温度场精准控制,减少能源消耗、降低污染物排放。四是设计开发了高效的“风流回热利用系统”,将带式焙烧机焙烧过程产生的各梯级热能高效利用,实现球团干燥、预热、焙烧等不同工艺过程能量的合理匹配和高效利用。五是开发研制了球团内配碳技术,可以将钢铁厂炭素粉尘及焦化粉末作为能源,实现固体废弃物的资源化、高效化综合利用,还可以提高球团焙烧质量,降低工序能耗。
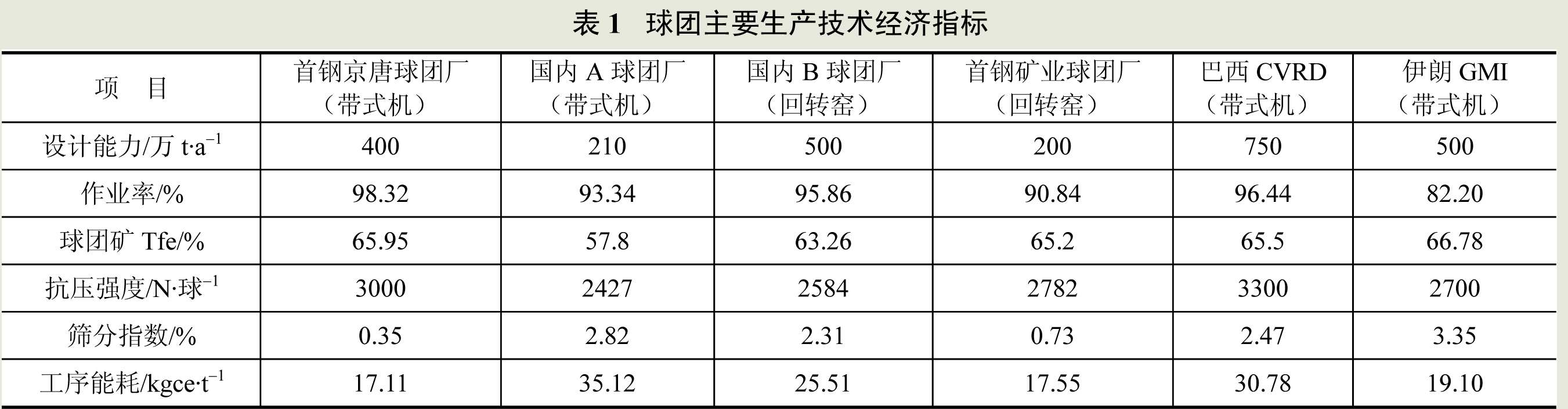